The horizontal mortiser has a router mounted on its side, and a workpiece attached to a multi-axis sliding table. This type of machine is best for floating tenons, which are created when two pieces of wood have corresponding mortises that must be attached via a third piece of wood. Chain models are best for large scale construction projects.
Furnituremakers discuss the value of a multi-router and compare it with other equipment options. August 21, 2006Question
We are looking at the Multi-Router for furniture construction. Anyone using the machine have any comments that would help us make a wise decision?
Forum Responses
(Furniture Making Forum)
From contributor A:
I'm familiar with most of the slot mortisers out there. All the shops around me use such machines as Griggio, Paolini, etc. - even a couple of Multi-Routers, so I've had a chance to try most of them. For that kind of money I'd be looking at full size units. I favor the use of loose tenons and even if I owned a Multi-Router I would still favor the loose tenons as far as speed and accuracy versus the bells and whistles of the Multi-Router. The horizontal slot mortiser was invented in the 50s in Europe. I like the lower rpm of the slot mortiser as it provides a nice option of being used as a doweling machine.
From contributor B:
I have a Multi-Router and love it! If you do decide to buy one you can make an offer on one on an on-line auction.
From the original questioner:
Are the full size units more accurate than the Multi-Router? I will bid on one at auction, unless they have a problem with accuracy.
From contributor B:
I have never used one of the bigger slot mortising machines but I couldn't be more pleased with the accuracy of the Multi-Router! I think with any of these machines it will take some playing with to learn how to get the best setup but I get thru it quite quickly. I also don't mind spending a little money to have a machine shop make a special fixture or setup gage that I use often enough to justify the $75.00 0r $100.00. Notice that this Multi-Router has pneumatic clamps. They also make a big difference in time. I have mine setup with a foot operated valve so both hands are free to set the work piece. I do all my face frames with it and some pieces get up to 8 feet long. These clamps hold the piece very tight to the table. Also I agree about the bells and whistles of the Multi-Router. I have the templates for the tenon making but rarely use them over the loose tenon process. It's quicker to set-up for one mortise and machine both parts for a loose tenon than to also have to set-up for the tenon. Feel free to ask if you have any questions on making set-up's.
From contributor A:
I've used the Multi-Router as well and the accuracy is fine. I prefer the standard horizontal slot mortiser for a couple of reasons. Bigger machines, so bigger pieces can be mortised. My favorite reason is the rpm. Typically slot mortisers run around 3,600 rpm. The plus of having a horizontal drill is well worth the money in my book and it doubles as a doweling machine. Some units have an indexed bar on them for using the doweling feature.
I know of folks using the Grizzly G0540 horizontal drill as a slot mortiser, $299.00. The Laguna/Robland mortiser - the mortise table from the combo machine – is around $600. Build your own stand and mount a router or even better mount a jackshaft and use a regular motor so you can use the lower rpm. The unit comes with the mortise chuck. The Rojek slot mortiser is around $1,600 and is available with the index bar feature. Commercial units such as Bini, Paolini, Griggio, Laguna, etc. a bit more than the JDS but heavier. There are also the homemade versions - old handmills from the metal working industry can be converted into a slot mortiser. Some even have collet chucks so less conversion is involved. Outdated machines can be often gotten at scrap prices.
From the original questioner:
You both have made some good points. I like the idea of having a heavy machine (less vibration). I also like the idea of the horizontal drill. I never thought about the scrap iron pile though. I think I will check out some of the used dealers in our area and maybe build a good heavy unit.
Plans Multi Slot Mortising Machines
From contributor B:
There is no question the Multi-Router is lighter weight than many of the other machines. Be sure to consider the volume of mortising you need to do. Also I have used it to cut mortises for house entry doors and I don't recommend it for that. You simply can't mount a heavy duty enough router for it - a slower rpm would be better for that type of work. I'd like to have a chisel mortiser for that purpose.
From contributor A:
Here's an example of a converted handmill. Most handmills don't have collets so some converting would be in order bit not really too difficult. Related web page: Handmill Mortiser
From contributor C:
Does anyone have an experience with the Grizzly g0540? I really want the Multi-Router but it’s a lot of money. For $299 the Grizzly seems worth a shot.
Delta Mortising Machine
From contributor A:
I've talked with several folks using the G0540 and heard positive things. Alternatives are in my previous post such as the Laguna/Robland. Also see FineWoodWorking #141 for a low budget, build-your-own. I know of someone who built a similar one and it works great. Also in the last years FWW Shops and Tools issue is one made using T track. There is no reason to not have a slot mortiser no matter what your budget. We use 2 flute HSS endmills in our slot mortiser which runs at 3,600 rpm.
From contributor D:
The Multi-Router is overpriced. My thousand pound mill machine with 2 horse motor was less money new than the 99 pound Multi-Router with no motor. Having said that, I would buy the Multi-Router again with no hesitation. I originally looked at the Hoffman machine to use their butterfly splines, especially on miter joints and crown molding. But it is not cheap either and that is the only function of the machine. I thought the Multi-Router would be more versatile; it could work for the splines as well as doing M&T and dovetails. I don’t have any of the templates for the machine yet as I prefer loose tenons and it does a great job for these. At first I was disappointed doing the splines, mostly because of getting things set up but after adding a scale to the X and Y axis, set up is now easy, accurate and fast. It also makes it much easier to cut mortises. I made a suggestion to John at JDS to add this feature to the machine but don’t know if he will entertain the idea or not. I just finished a set of cabinets and the butterfly splines worked great on the crown molding. I don’t know about the other machines but having the ability on the M-R to do different angles is a big item for me. If anyone has this machine or acquires one at some time, I think you will be really pleased if you add the scale on the X and Y axis. Since my eyes don’t see as well as they once did, I also add a Starrett scale to the Z axis so it would be easier to read. These are my opinions only and may not be useful for others.
From contributor B:
I sure am glad I have my Multi-Router already! The idea for adding scales to the X, Y, and Z axis is a good one but if JDS decides to add it as a part of the machine, this suggestion just made the already over priced machine another $300.00 over priced. Seriously though, would you care to share how you assembled your scales to the machine, with the rest of us owners of Multi-Routers? I am very curious!
From contributor D:
The upgrade to my Multi-Router was not a high tech procedure, as I needed something quickly that would work using the Hoffman splines in some crown molding that had to be finished. I wasn’t sure that it would solve my problem but it works great for me.
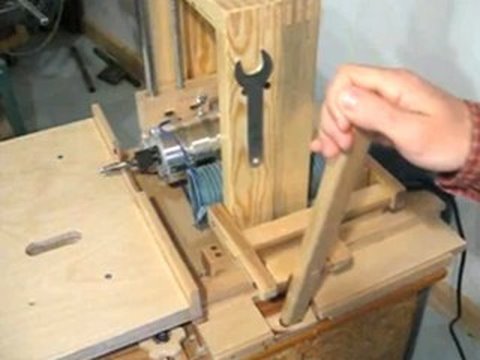
On the X axis, a piece of aluminum L stock 1/8” x 1 by 8” was screwed to the Y carriage housing using the same procedure as above with the flat side up. Another 8” piece of tape was stuck to the top of the L bracket. Another pointer like the one described above was glued to the X carriage housing using the Loctite in a position just barely above the tape. The tape was positioned so the pointer was on an even number when the table was zeroed to the vertical table. Now I don’t have to try and see the scribe marks on the table to get them aligned, just set the pointer on the scale.
Now when applying two splines to a miter joint, one edge of the stock is set on the table scribe line, move the pointer over the desired distance from the edge for the first dovetail cut, then move to the distance needed for the second dovetail. Then repeat the steps for the joining stock. It has worked perfectly for me and is quick and simple. It also makes it much easier to cut mortises using the tape as a reference. Don’t have to try and match up pencil lines on the stock any more.
My next modification is to put a steel plate on the base of the machine. This will permit placing a magnetic holder for my dial indicator if a need arises for this level of accuracy. I know some will question the need for this level of accuracy in woodworking but I have a Jointech fence and a precision router lift that have this capability and it is surprising how often I adjust just a few thousandths to get a better fit.
Used Mortising Machines For Sale
I made do with materials on hand and it works but it could be refined and made to look nicer if one took a little more time. It would also be nice to have the X axis scale read 0 to 4 each side of center. This is a terrible job of explaining but I’ve never been blessed with that talent. I will be glad to try and answer any question you may have. I would be very interested to hear how you, and others, do yours. If there are modifications, tricks or shortcuts that are used, please share.
From contributor B:
I'm getting most of what you are saying. I am going to look at this for my set-up.
The comments below were added after this Forum discussion was archived as a Knowledge Base article (add your comment).
Comment from contributor E:
I too have a multi-router, which frustrated me to some degree as I found its set up too hit and miss. I now use a vernier caliper to set up the stylus position relative to a newly machined spot on the top of the stylus casting. This means that I can more easily center a tenon on any stock size.
I also found that the original A, B and C tenon templates that JDS supply don't offer any fine adjustment. I have designed my own ones (in more sizes than the original set) which I get CNC machined and hard anodized. These templates mean that I can fine tune the fit of a tenon in a mortise, even if I have sharpened a cutter, leaving it smaller in diameter.
Would you like to add information to this article?
Interested in writing or submitting an article?
Have a question about this article?
Have you reviewed the related Knowledge Base areas below?
Would you like to add information to this article? ... Click Here
If you have a question regarding a Knowledge Base article, your best chance at uncovering an answer is to search the entire Knowledge Base for related articles or to post your question at the appropriate WOODWEB Forum. Before posting your message, be sure to review our Forum Guidelines.
Questions entered in the Knowledge Base Article comment form will not generate responses! A list of WOODWEB Forums can be found at WOODWEB's Site Map.
When you post your question at the Forum, be sure to include references to the Knowledge Base article that inspired your question. The more information you provide with your question, the better your chances are of receiving responses.
Return to beginning of article.
Refer a Friend || Read This Important Information || Site Map || Privacy Policy || Site User Agreement Letters, questions or comments?E-Mail us and let us know what you think. Be sure to review our Frequently Asked Questions page. Contact us to discuss advertising or to report problems with this site. To report a problem, send an e-mail to our Webmaster Copyright © 1996-2020 - WOODWEB ® Inc. All rights reserved. No part of this publication may be reproduced in any manner without permission of the Editor. Review WOODWEB's Copyright Policy. The editors, writers, and staff at WOODWEB try to promote safe practices. What is safe for one woodworker under certain conditions may not be safe for others in different circumstances. Readers should undertake the use of materials and methods discussed at WOODWEB after considerate evaluation, and at their own risk. WOODWEB, Inc. 335 Bedell Road Montrose, PA 18801 Contact WOODWEB |
How to cut mortises accurately with a hand-held router, a straight bit, a template guide and a few scraps.
There are many ways to make mortises — and just about as many tool options. A plunge router is one of the best choices, because you can accurately control the depth of cut, and the machine delivers clean and precise results. Here’s a simple, dedicated jig you can make quickly for cutting mortises of a specific dimension with your plunge router. Its top plate has a slot to fit a template guide mounted to the router, so cutting accuracy is assured. And, a fence attached beneath the jig’s top plate provides a stout clamping surface for your workpiece, whether you secure the jig and workpiece in a bench vise or with hand clamps. Here’s how to make and use the jig.
Step 1: Since this mortising jig is dedicated to a specific-size mortise, laying out your mortised workpiece is the first step in building the jig. Everything follows from the mortise proportions. Mark the length and width of your intended mortise with a square, and extend layout lines a short distance onto the adjacent (un-mortised) faces of the workpiece to serve as reference lines later (see Photo 1).
Step 2: A second important piece of information you’ll need is the outside diameter (O.D.) of the screw-in template guide you’ll use in your router with this jig, as well as the diameter of the appropriate router bit. Here we’re going to use a 5/8-in. O.D. template guide around a 1/4-in. carbide spiral upcut bit. (Note: a conventional two-flute straight bit would also work fine.) The difference between the template guide’s O.D. and the router bit diameter is called the offset. You can measure it (see Photo 2), but a more accurate method to find offset is to simply subtract the bit diameter from the template guide O.D. — in our case, 5/8-in. minus 1/4-in. equals 3/8-in. of total offset. Divide this number in half to find the offset on either side of the bit; in this example, it is 3/16-in.
Step 3: For the top plate of your jig, choose a piece of 1/2-in.-thick scrap that measures 4- to 6-in. wide and about 10- to 12-in. long. Rip a strip from one edge that is exactly as wide as your template guide’s O.D. or slightly wider (see Photo 3). The strip won’t work for the jig if it is any narrower than the template guide — it establishes the width of the jig’s slot.
Step 4: Now rip the top plate of your jig in half, and crosscut the spacer strip in two. Measure the length of your mortise layout from Step 1, and add to its length the total amount of offset (in our case, 3/8-in.). This number determines the total length of the jig slot. Mark the slot locations on your top plate workpieces; centering the slot on the top plate is a good idea. Form a “sandwich” of top plate pieces and spacer strips — spread open to the overall slot length — to create the jig slot. Glue and clamp the top plate assembly together (see Photo 4). When the glue dries, trim off the excess spacer strips from the ends of the plate.
Step 5: With the template guide and router bit installed in your plunge router, turn the router bottom-side up and fit the template guide’s bushing inside the jig’s slot. Plunge the router base until the bit passes through the plate so you can access it as a reference for measuring. Now use a combination square to mark long layout lines on the plate that indicate the width of the mortise. Then slide the bushing from one end of the slot to the other to mark the length of the mortise. When marking the plate, always reference from the outside edge of the router bit (see Photo 5).
Step 6: At this point, you can install the jig’s fence. To locate the fence’s position on the top plate, align the mortise “width” layout lines on your workpiece with the corresponding lines you just drew on the top plate. Draw a short layout mark on each end of the plate that’s even with the edge of your workpiece to set the fence location. You can position these layout marks either to the left or the right of the jig slot; it doesn’t matter. A bench vise can be helpful for holding the mortised workpiece steady as you align it with the plate for marking (see Photo 6).
Step 7: Select a piece of scrap several inches longer than your jig’s top plate to use for a fence. Clamp it beneath the top plate, aligned with the layout marks you drew in Step 6. Fasten the parts together with countersunk wood screws (see Photo 7). The extra fence length on each end of the plate can be helpful for clamping purposes.
Step 8: The short reference lines you drew onto the un-mortised sides of your workpiece will now come in handy for positioning it in the jig to prepare for routing (see Photo 8). Clamp the workpiece and jig together securely.
Step 9: Use the stepped turret on the router base to set up the first and subsequent depth cuts to excavate the mortise depth you need (see Photo 9). With each pass, you can either push or pull the router along the slot to clear the waste — the feed direction doesn’t matter. Make sure to remove no more than about 1/8-in. of material with each pass, especially when routing hardwood (see Photo 10, below). Use compressed air or a shop vac to keep the mortise area and jig slot clean.